Print Settings Overview
The V-One is an excellent tool for dispensing high viscosity fluids. You can expect to get high quality printing out of the box or by making some small adjustments to the printing settings.
Below is a brief explanation of the different settings found on the V-One software. Contact [email protected] for some extra tips and tricks.
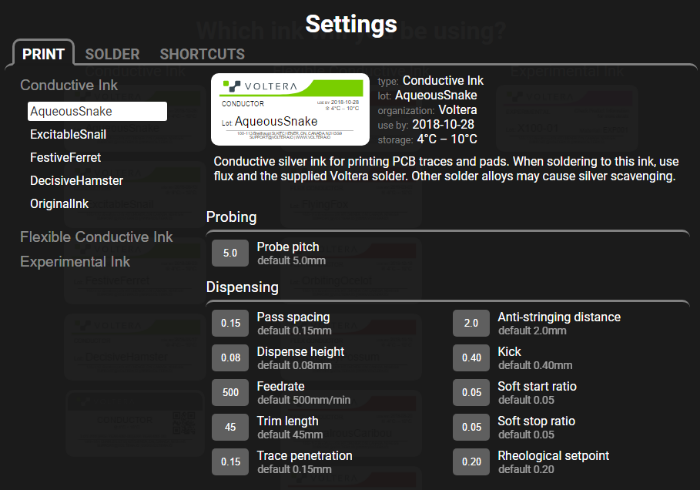
Pass spacing
From 0.10 - 1.00 mm
Controls minimum center-to-center distance between two adjacent lines printed with the V-One. If you’re working with a customer material, the main reason to adjust this is if you’re using a different nozzle size. But the width of the fluid dispensed will be different based on a few criteria that are all intertwined; material slump, print height, and nozzle diameter. The goal of changing this setting is to make sure that adjacent passes that make up a single feature don’t have any gaps between them and don’t overlap too much.

Dispense height
From 0.01 - 1.00 mm
Set the distance between the tip of the nozzle and the substrate surface during printing. The V-One dynamically corrects the height based on the probed height map to maintain this value as constant (+/- about 20um). If you’re working with a customer material, the main reason to adjust this is to ensure that your material is properly adhering to the substrate. Some materials need to be pressed into the substrate and others need space to flow out.
Feedrate
From 0 - 600 mm/min
This indicated the XY-axis travel speed during dispensing. It does not affect travel speed when moving between features. If you’re working with a customer material, the main reason to adjust this is to make sure that your material is adhering to the substrate and the resolution of the features fits your application.
Trim length
From 1 - 9999 mm
Maximum distance the printer will dispense for before it stops and re-pressurizes the cartridge (by applying another 'Kick'). The reason is that pressure within the cartridge decreases slowly while dispensing, so the V-One needs to compensate for the flow rate and re-pressurize between traces. The main reason to adjust this is if the material is more compressible and needs to be re-pressurized sooner or it’s less compressible and can wait longer to be re-pressurized.
Trace penetration
From 0.00 - 5.0 mm
To make sure traces and pads connect properly, the V-One plans ahead so that traces will travel a small distance into a pad. This determines how far in the trace goes. The main reason to adjust this is if the material you’re working with does not work well with overlapping and needs to be minimized as much as possible.

Anti-stringing distance
From 0.1 - 5.0 mm
Depending on the surface energy of a fluid, it might prefer to stick to the nozzle than the board, which produces 'stringing' when the nozzle raises. The V-One adjusts for this by traveling back over the feature to safely break the string, rather than allowing the string to break during raise/travel. If you’re working with a customer material, the main reason to adjust this is if you need a more extreme movement to break the surface energy of your fluid.

Kick
From 0.05 - 2.00 mm
This parameter controls the Stroke Length of the piston within the dispenser when dispensing, hence how much pressure is applied. This parameter, along with the rheological setpoint, are the most important for printing different fluids. Fluids that are highly compressible and viscous will need a large kick to initiate flow and force the fluid through the nozzle, while lower viscosity fluids need a smaller Kick. Incompressible and low-viscosity fluids will only need a very small Kick to initiate flow.
There is often confusion regarding Kick and the +/- settings - while both control the piston, they do different things. The Kick is the MAXIMUM displacement of the piston when starting a dispense, while +/- adjust the relative starting position of the piston.

Soft start / stop ratio
From 0.00 - 1.00
These control the amount of the kick that is applied after starting to dispense a feature (soft start) and the amount of the kick retracted before ending a dispensed feature (soft stop). This is represented as a ratio of the Kick value, ex. 0.10 would be 10% of the 0.35mm Kick value. Due to compressibility of the fluid and mechanical factors (like speed of the motors) there is a delay between when the Kick is initiated (pressurization starts) and when the flow rate reaches the correct level to start a line or other feature. This is similarly true for terminating the flow rate/releasing pressure. These parameters are used to appropriately compensate for this. These don't typically need to be adjusted except for particularly compressible or viscous materials.

Rheological setpoint
From 0.00 - 1.00
As mentioned above, this parameter and the Kick are the two most important parameters for printing consistency and quality. While Kick controls the amount of pressure applied to the fluid, Rheological Setpoint controls how the V-One compensates for the flow rate over time. For high-viscosity compressible fluids (like the conductive ink or solder paste), they tend to taper their flow rate slowly over time. The parameter is quite sensitive, so make small adjustments as necessary. If you see that your fluid is running out over the course of your print, increase the setting by 0.01. Similarly if you notice your fluid starting to build up over the course of your print, decrease the setting by 0.01.
Rheological Setpoint for Incompressible / low-viscosity fluids:
For incompressible fluids, this parameter is used in a slightly different way - you want to adjust it to account for total fluid volume you want dispensed each stroke. However, for reasons to do with the typical use-case and the algorithm, this approach will only work for printing many identical features - meaning if you're printing a circle that is 0.5mm in diameter, vs. one that is 0.3mm in diameter, you'd need to change the rheological setpoint to get the same fluid volume dispensed.
Last updated
Was this helpful?